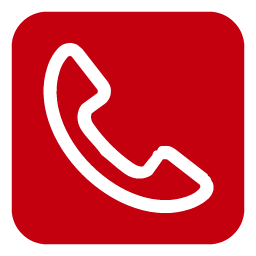
Telephone consultation
400-102-3850
Coal chemical industry
Production of medium and low boiling fusel oil from coal to methanol
Background technology
Methanol is one of the important basic organic raw materials, which is used to produce a variety of organic products such as methyl chloride, methylamine and dimethyl sulfate. It is also a raw material for pesticides (insecticides, acaricides), pharmaceuticals (sulfonamides, oxytetracycline, etc.), and one of the raw materials for the synthesis of dimethyl terephthalate, methyl methacrylate and methyl acrylate. At present, the production of methanol is mainly synthetic method, and the chemical reaction formula of synthesis is: 2H2 CO → CH3OH, and the raw materials are mainly derived from oil and natural gas. In recent years, as the price of oil and natural gas continues to rise, coal chemical industry has gradually received attention, through coal gasification purification to obtain synthesis gas, through low-temperature methanol washing to remove acid gas for synthesis of crude methanol.
In the typical process of crude methanol separation and refining, a four-tower separation and refining process is often used: a pre-distillation tower, a pressurized distillation tower, an atmospheric distillation tower and a methanol recovery tower. Crude methanol enters the pre-rectification tower, and the process water is sprayed at the top of the pre-rectification tower for extractive distillation. After removing light components (mainly non-condensable gas, dimethyl ether, etc.), the methanol and high boiling point components at the bottom of the tower enter the pressurized rectification tower after pressurization; the refined methanol after vapor phase condensation at the top of the pressurized rectification tower enters the reflux tank, and part of the refined methanol product comes out of the device; the methanol, high boiling components and water at the bottom of the pressurized tower enter the atmospheric tower, and the refined methanol product is extracted from the top of the atmospheric tower, and the side line is set below the feed plate. The extracted materials are mainly methanol, water and high boiling components, which enter the methanol recovery tower and then recover methanol, and the bottom wastewater enters the biochemical system for treatment. The recovery tower is equipped with a side line to extract low-boiling fusel oil to ensure the quality of refined methanol at the top of the recovery tower and the total alcohol content in the bottom wastewater. The bottom wastewater is sent to biochemical treatment. The low-boiling fusel oil extracted from the side line of the recovery tower is mainly composed of methanol, isopropene ether, n-hexane, ethanol, butanone, propanol, n-heptane, water, etc. The methanol content is related to the synthesis conditions, and the water content is 30 ~ 50wt.%. In this part of fusel oil, water molecules and each component form a variety of binary and multicomponent azeotropes, which are difficult to remove water by ordinary distillation, and increase great difficulties for further recovery of methanol in fusel oil.
Process flow
1, preheater; 2, concentration tower; 3, partial condenser; 4, superheater; 5, pervaporation membrane separator; 6, permeate condenser; 7, vacuum unit; 8, refining tower; 9, heat pump.
The low-boiling fusel oil extracted from the side line of the methanol recovery tower in the methanol refining section enters the concentration tower for concentration. The fusel oil vapor after preliminary dehydration in the concentration tower is distilled out from the top of the concentration tower, and part of the vapor is condensed for reflux in the concentration tower. The rest of the vapor is sent to the pervaporation membrane separator for separation to obtain 0.01 ~ 1wt.% fusel oil dehydration product vapor without condensation, the water and a small amount of organic matter in the liquid side solution pass through the pervaporation membrane in the form of steam to obtain the permeate, and the permeate is condensed and returned to the concentration tower, and the top product of the tower enters the pervaporation membrane separator. The steam of the dehydration product of the pervaporation membrane separator enters the refining tower in the form of vapor phase without condensation, and the methanol product is extracted from the top of the refining tower, and the residual liquid discharged from the tower kettle is used for further separation and recovery of organic components.
Synthesis gas to ethanol
Background technology
Ethanol is widely used in national defense chemical industry, medical and health, food industry, industrial and agricultural production. Ethanol production methods include biological fermentation and chemical synthesis. Among them, the production technology of ethanol from syngas by chemical synthesis is mature, and the production cost is significantly lower than that of grain route, which has strong competitiveness and broad development prospects. There are three types of syngas to produce ethanol, one is the direct production of ethanol from syngas, the other is the biological method of ethanol from syngas, and the third is the hydrogenation of syngas to ethanol by acetic acid. Regardless of the ethanol production method, aqueous ethanol is obtained. Due to the azeotropic point of ethanol and water, anhydrous ethanol cannot be obtained directly by traditional methods. At present, the production of industrial anhydrous ethanol mainly adopts the methods of azeotropic distillation, extractive distillation and adsorption separation, these traditional ethanol dehydration methods have problems such as complex process, high energy consumption and serious pollution.
Process flow
1, the first heat exchanger; 2, the first heat exchanger; 3, distillation tower; 4, reboiler; 5, overhead condenser; 6, superheater; 7, steam permeable membrane equipment; 8, heat pump.
Syngas undergoes multi-step reaction to obtain reaction products containing ethanol and water. Before entering the steam permeable membrane, the reaction products are separated in a rectifying tower, and the top or side of the last rectifying tower extracts ethanol steam with 0.1 ~ 30% water content; The water-containing ethanol steam enters the membrane equipment after overheating or passing through the heat pump, and is separated by the membrane module. The outlet (positive pressure side) of the membrane is the finished ethanol product with 0.01~1 water content.
Process advantages
The use of distillation-steam permeable membrane equipment coupling technology, the traditional process and new separation technology coupling, without azeotropic restrictions, without adding the third component, is a high efficiency, energy saving and environmental protection separation technology.
Coal to Ethylene Glycol By-product Ethanol
As an important petrochemical basic raw material, ethylene glycol is mainly used in the production of polyester fiber, polyester plastic, antifreeze, lubricant, plasticizer, etc. It is also used in explosives, coatings and inks and other industries, and it can be derived from a variety of 100 chemicals with a wide range of uses. For the production of polyester, antifreeze, fine chemical products accounted for about 94% of the total consumption, 2. 5%,3. 5%.
Indirect synthesis of ethylene glycol technology mainly includes methanol dehydrogenation dimerization method, dimethyl ether oxidative coupling method, glycolic acid method, formaldehyde condensation method, formaldehyde hydroformylation method and oxalate hydrogenation method, of which oxalate hydrogenation method is currently the most widely used and widely studied coal-to-ethylene glycol technology.
The coal-based oxalate method produces syngas by coal gasification, and at the same time uses alcohols to react with N2O3 to generate nitrous acid esters; nitrous acid esters are oxygen-coupled on Pd catalysts to obtain oxalic acid diesters; oxalic acid diesters are subjected to catalytic hydrogenation to produce ethylene glycol. Among them, the most studied alcohols are methanol and ethanol.
The process of oxalate hydrogenation to produce ethylene glycol is mainly composed of esterification unit, carbonylation unit, hydrogenation unit and ethylene glycol refining unit. The function of the esterification unit is to oxidize the NO produced by the carbonylation unit and the methanol ME obtained by the hydrogenation unit to obtain methyl nitrite. The role of the carbonylation unit is to carry out the catalytic coupling reaction of CO and methyl nitrite MN to obtain the intermediate product dimethyl oxalate DMO, while the reaction to generate NO is returned to the esterification unit through the separation system. A small amount of dimethyl carbonate DMC produced by the unit is separated from DMO by the separation system. The function of the hydrogenation unit is to hydrogenate DMO to obtain crude product of ethylene glycol EG, and at the same time react to generate ME, which is returned to the esterification unit by the ME separation system. A small amount of hydrogenated crude products such as methyl glycolate MG, ethanol Et, water and 1,2-butanediol are by-produced in this unit. The refining unit is to refine the crude EG product to obtain polyester grade EG and frozen grade EG products.
In addition to polyester grade EG and refrigeration grade EG products, the process finally produces a by-product consisting of ethanol Et, methyl glycolate MG, water and 1,2-butanediol. For an industrial plant with an annual output of 200000 tons of ethylene glycol, the ethanol by-product produces about 10000 tons. If the ethanol by-product can be recovered, the profit of the process can be effectively improved.
Process flow
1. First heat exchanger; 2. First heat exchanger; 3. Distillation tower; 4. Fractionator; 5. Superheater; 6. Steam permeable membrane equipment.
The ethanol by-products produced by the process are first separated in a rectifying tower to remove high boiling point impurities such as methyl glycolate and 1,2-butanediol in the by-products. Ethanol vapor containing a small amount of water is taken out from the top of the rectifying tower. The ethanol vapor containing water enters the membrane equipment after overheating or passing through a heat pump, and is separated by the membrane module. The membrane outlet (positive pressure side) is the finished ethanol product.